Toyota’s digital revolution takes a captivating form in their newest offering: A virtual tour of their automotive manufacturing process.
The experience emphasizes the efficient use of materials, attention to detail, and the seamless integration of human skills with technology in producing a vehicle with around 30,000 parts on average. The virtual tour is divided into five main parts for the assembly of a vehicle plus additional sections for power unit creation and Toyota’s production philosophy.
The process starts with different types of steel plates, each one selected for a specific purpose. Harder materials protect the car’s occupants, while softer ones are used to absorb impact. Impressively, a single 2.5-kilometer roll of steel can contribute to making 300 vehicles.
Next, the tour showcases the car body creation process, which combines speed and precision. Each stage takes only three seconds and involves 1,600 tons of pressure. Despite the high-tech nature of the process, the human touch remains vital, with manual adjustments made down to the 1/1000 mm level for perfect alignment.
Toyota makes it a point to achieve minimal waste in the manipulation of steel parts and have achieved a system of prepping the stamped steel for a Mixed Model Production line.
Once a particular model’s stamped parts are complete, it then moves to the welding process. Individual steel parts, such as body side panels are welded by robots using spot welding, with close to 4000 places in each car to shape the body, and additional 500 more places to provide structural strength.
Toyota employs multiple welding technologies such as spot, arc, and laser welding in the production of a car, each applied based on the specific needs of the area being welded. The use of special robots for additional welding points underscores Toyota’s commitment to vehicle strength and safety, but some steps such as arc welding, an area out of reach by the robots, are carried out by skillful craftsmen.
Doors, hoods, and trunk lids are then placed onto the shell. It’s amazing to know that on the assembly line, doors are intentionally displaced, as the addition of window motors, glass, insulation, and other door parts will eventually weigh the steel door down into the correct position.
After inspection, the shell goes through a 7-step painting process outlined in the tour. From cleaning, to priming, painting and final inspection, the shell goes through corridors of robots and mechanized rails in what can only be described as a triumph of industrial automation.
Close to the end of the production line, the assembly stage utilizes a just-in-time delivery system, ensuring parts arrive exactly when needed. This stage involves assembling around 3,000 components per vehicle, from installing the engine to fitting door handles. Toyota closely works with over 60,000 parts suppliers in a collaborative process to ensure parts are manufactured properly and are delivered when needed.
Then starts the human process of assembling each and every little part that goes into a Toyota vehicle. With the aid of robotics, Toyota craftsmen skillfully install all the other required modules to make the car. Throughout this process, Toyota places a high value on their employees’
well-being, fostering a work environment based on continuous improvement, known as “Kaizen.”
The final stage in the creation of the vehicle involves inspection and shipping, where each car that rolls off the assembly undergoes a 1,500-point quality check before being sent off to shipping. In Japan alone, more than 10,000 cars are manufactured daily before being sent to their distribution networks.
To delve deeper into the production processes, the tour highlights four critical stages into the creation of the engines or power units: Casting, forging, machining and assembly, each stage underscoring the meticulous attention to detail, craftsmanship and dedication to continuous improvement that defines Toyota.
Casting unravels the transformative journey of molten metal into tangible designs. It’s a delicate dance of heat, time and material characteristics, revealing the intrinsic complexity of shaping metals and the determination required to perfect the technique for mass production.
Forging, a significant stage for creating components like the crankshaft, emphasizes the profound influence of human skill and wisdom. The stage beautifully demonstrates the seamless integration of traditional craftsmanship with modern technology, reinforcing Toyota’s belief in the irreplaceable value of human skill.
The machining process displays Toyota’s unwavering commitment to perfection, seen in the production of precision engine parts with a tolerance of 1/1000th of a millimeter. The controls in place to prevent the production of defective parts embody Toyota’s stringent quality assurance.
Lastly, the assembly process stands as a testament to Toyota’s people-first philosophy. They focus on simplifying manual operations and enhancing accuracy while ensuring an inclusive environment that accommodates people with disabilities.
Toyota’s dedication to “Kaizen” fosters a culture of continuous improvement, reflecting their unwavering commitment to the development of people and the production of ever-better cars.
The last part of the virtual tour paints a picture of how Toyota lays down the foundations of its production processes. The Toyota Production System, a cornterstone of Toyota Motor Corporation’s manufacturing philosophy, is centered around enhancing product quality, ensuring affordability, and reducing workload on employees.
It focuses on eliminating three inefficiencies: Muri (overburden), Mura (unevenness or irregularity), and Muda (non-value added activities or waste). The goal is to produce flawless products and to manufacture or transport only what’s needed, when it’s needed, and in the exact quantity needed.
TPS is underpinned by two primary concepts: Jidoka (or Autonomation) and Just-in-Time. Jidoka aims to prevent defects by automatically halting machines when abnormalities are detected, thereby increasing productivity and reducing the need for constant human monitoring. The system employs fail-safe devices, or ‘Poka-yoke’, to alert workers of problems and prevent defective products.
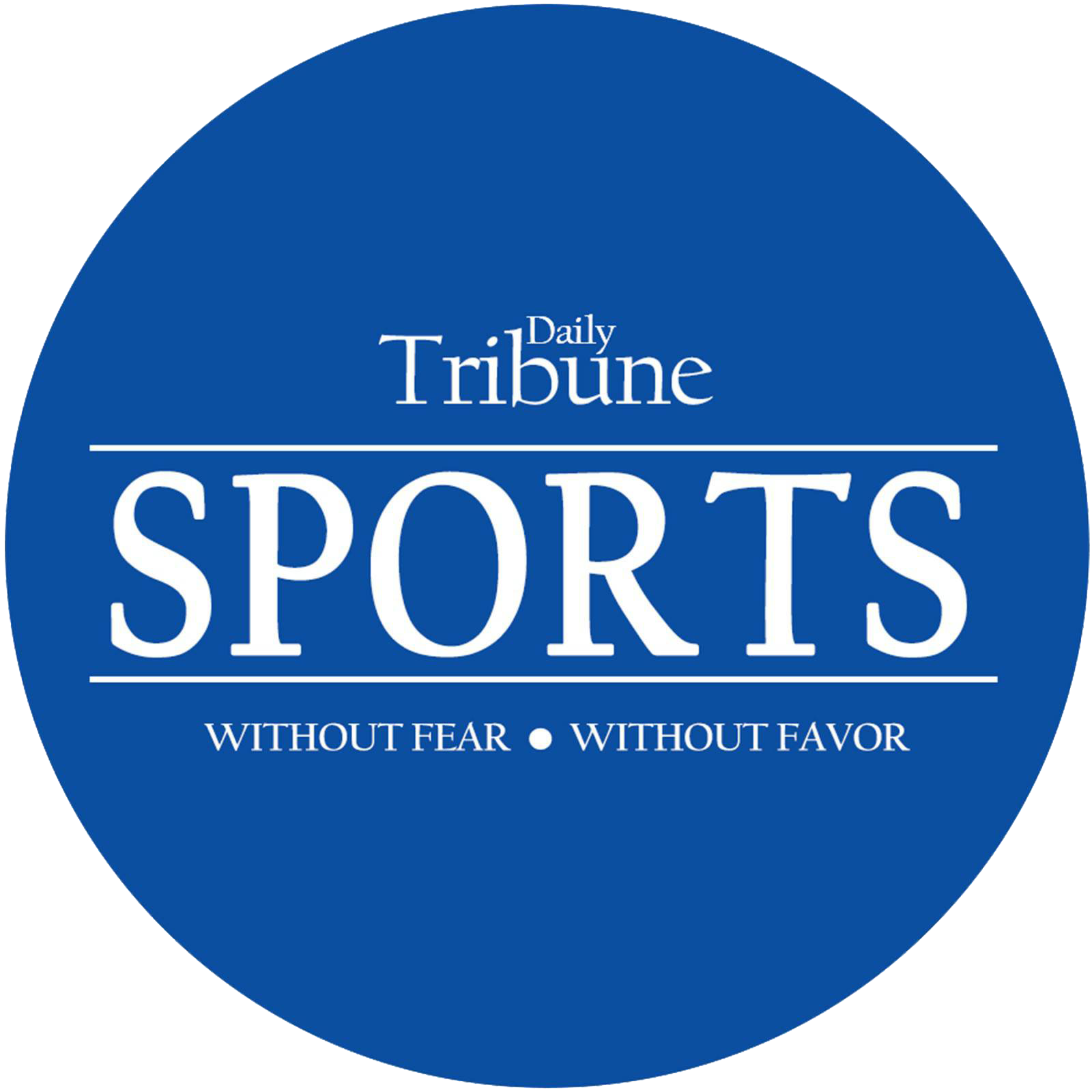